What Does MRP Stand for? What Are the Differences versus ERP?
Want to know what MRP stands for? This article discusses the differences between MRP and ERP systems, and why they are both important to small manufacturing businesses.
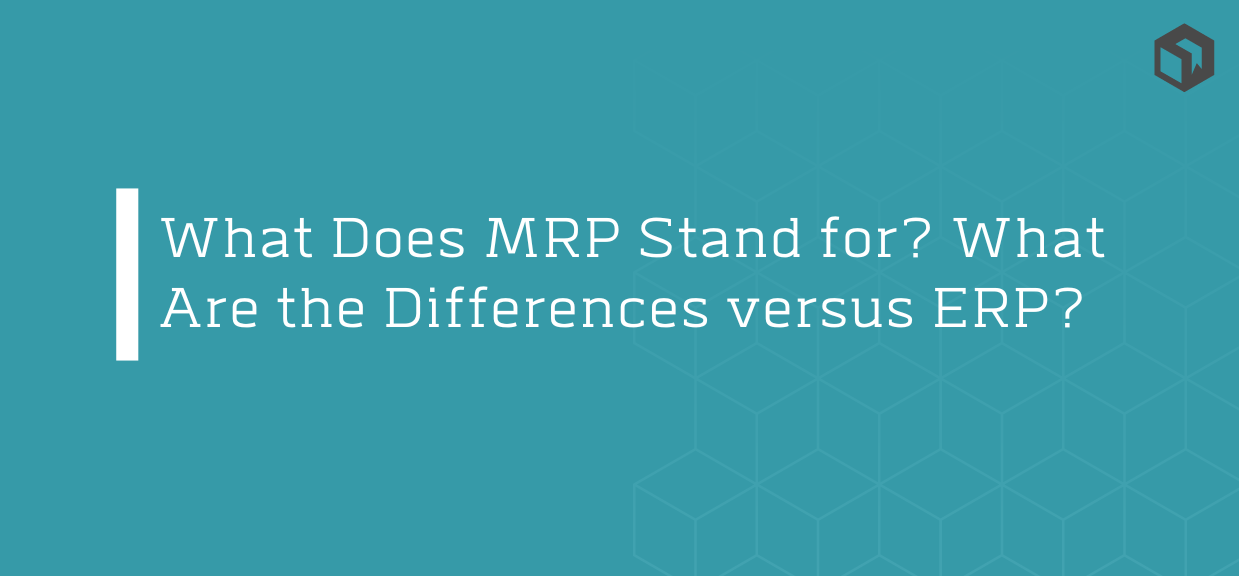
Materials Resource Planning (MRP) and Enterprise Resource Planning (ERP) are both terms often used in manufacturing businesses. As someone new to the manufacturing and operations side, these terms can be understandably confusing.
Both MRP and ERP systems both help businesses manage their resources effectively, but there are some key differences between the two. In this article, we’ll dive into the differences between MRP and ERP systems so you can better understand what these terms mean and also see which one is best for your business.
Need to get your raw material and product inventory under control?
Try Craftybase - the inventory and manufacturing solution for DTC sellers. Track raw materials and product stock levels (in real time!), COGS, shop floor assignment and much more.
It's your new production central.
What does MRP stand for?
In a nutshell, MRP stands for “Materials Resource Planning”. It’s essentially any system that helps businesses plan and manage their raw materials, manufacturing, and finished products. MRP systems help manufacturing businesses by offering different features designed to keep track of inventory levels, planned production, and purchasing.
The term MRP is also sometimes also used for “Manufacturing Resource Planning”, which is an almost identical concept. Manufacturing resource planning is a term that encompasses all of the resources needed to manufacture a product, not just materials. It does this by looking at and tracking your entire manufacturing business - i.e. capacity planning, tooling, and workforce planning.
MRP is also used as an acronym for “Material Requirements Planning” which again has a fair amount of overlap with the MRP definitions above - it’s mainly focused on the actual procurement of materials based on predicted manufacturing activity (which is usually managed using a master production schedule).
What does ERP stand for?
ERP stands for “Enterprise Resource Planning”. ERP systems are used to manage all of the resources of a business, not just materials. This includes things like financials, HR, and supply chain management. ERP systems usually have modules that can be customized to the needs of the specific business.
One of the key benefits of ERP systems is that they give businesses a holistic view of their operations. This can help businesses identify inefficiencies and areas for improvement across the complete supply chain.
So, what are the key differences between MRP and ERP?
To recap, MRP systems are focused specifically on materials and inventory, while ERP includes all aspects of business operations, from finance to manufacturing to human resources.
Both MRP and ERP can help businesses optimize their production processes, reduce costs, and improve customer satisfaction. However, MRP is better suited for businesses that have very specific needs in terms of managing their materials and inventory, while ERP is a more comprehensive solution that can address a wider range of business needs (and can therefore be much more expensive to implement).
What features are usually found in ERP software?
As we have discussed, ERP software typically includes wider-ranging features for managing different aspects of business operations, such as finance, manufacturing, human resources, and supply chain management.
These features (or “modules”) usually fall into the following categories:
Financial management
This includes features like accounting, financial planning, and reporting.
Human resources management
This area involves payroll, employee tracking, and performance management (i.e. KPIs).
Customer relationship management
This involves tools that handle sales and marketing automation, customer service, and support.
Manufacturing
This includes MRP features like production planning, quality control, and inventory management.
Warehouse and location management
This is another area that overlaps with MRP software and includes procurement, warehousing, and transportation.
Project management
This includes features like task tracking, project planning, and resource allocation.
ERP software options
There are a number of software options available for small manufacturers looking for an ERP system. Some popular options include:
- SAP Business One
- Microsoft Dynamics 365 Business Central
- Acumatica Cloud ERP
- Sage Intacct
- NetSuite ERP
ERP systems can be very expensive to implement, especially for small manufacturing businesses. The cost will depend on a number of factors, such as the size of the business, the complexity of its operations, and the specific modules that are included in the system.
One way to reduce the cost of an ERP implementation is to choose a cloud-based solution, which can be more affordable than on-premise software.
What features are usually found in MRP software?
MRP software is typically used by businesses to manage their materials and inventory more effectively. The features found in MRP software can vary depending on the specific product and price range, but some common features include:
Raw materials management
Features to help businesses keep track of their raw materials, finished goods, and inventory levels. This can include sub-assembly tracking (components that make up parts of the finished product)
Inventory control
Track real-time levels for raw material, sub-assemblies and finished product inventory levels, and also stock movements between locations.
Production planning
A suite of features to allow manufacturing businesses plan and schedule their production processes using both historical and future data, in order to create a master production schedule.
Capacity planning
This module helps businesses plan and manage their capacity needs, based on past data and future activity.
Quality control
This area helps businesses ensure that their products meet quality and regulatory standards. Features like batch and lot tracking and expiry dates are usually core parts of the QC featureset.
Cost management and analysis
This set of MRP features helps businesses track and analyze their costs. This can include pricing guidance, profit and margin calculations, COGM calculations and overall inventory and overhead expenditure tracking.
Materials sourcing and procurement
Allows small manufacturers to track where they source their raw materials from so that they can optimize the purchasing part of the supply chain.
Reporting and analytics
Features that provide businesses with the ability to generate reports and perform in-depth analyses on their inventory, stock movement and costing data.
MRP software options
There are a number of software options available for small manufacturers looking for an MRP system. Some popular options include:
Craftybase MRP
This cost effective MRP system is designed specifically for small manufacturing businesses and really shines for workflows where products are made in-house.
Features raw material, COGS, multilevel bill of materials, complex sub-assembly production and location management, it’s a really tidy all-in-one solution for makers.
Katana
This MRP system is designed for “ambitious manufacturers looking to scale” and offers a number of plans suitable for small manufacturing businesses at different stages.
MRPeasy
Another good MRP system for manufacturing businesses of all sizes, they have a number of different pricing options designed to meet the needs of growing businesses.
ERP vs. MRP: Which is right for your small manufacturing business?
The best way to determine whether ERP or MRP is right for your business is to assess your specific needs and requirements: both now and with your future business goals in mind.
As a rule of thumb, ERP systems are typically more expensive and require more training to use effectively, while MRP systems can be less expensive and easier to implement.
If you have a small manufacturing business that makes products in-house, then MRP might be the best option for you due to its more approachable price points and its primary focus on inventory management features. You can then add systems to handle the different functions of your business as it grows.
However, if you are looking to scale your business significantly and can afford the overhead of an ERP system, you may like to go with a more holistic solution that includes out-of-the-box ways to manage your staffing and HR needs.
Introducing Craftybase: Your Small Business MRP
If you are a small in-house manufacturer, Craftybase is your cost effective MRP solution.
Craftybase features a range of robust inventory management and manufacturing tools, designed to get you back to doing what you do best: growing your small business and making the products you love to make.